Robotics In Manufacturing And How It’s Transforming Industry Standards
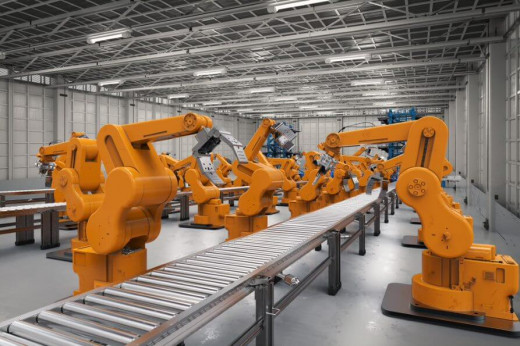
Robotics In Manufacturing And How It’s Transforming Industry Standards
Are you familiar with the term "robotics in manufacturing"? If not, then prepare to be amazed! Robotics has made a significant impact on the manufacturing industry, transforming it into a more efficient and productive sector. The use of robots in the production line has become increasingly popular over time, and it's easy to see why. With improved accuracy, speed, and safety measures, robotics is rapidly changing industry standards for good.
In this blog post, we'll take an in-depth look at how robotics is revolutionizing modern-day manufacturing processes. So buckle up and get ready for a fascinating ride through history to the future of robotics in manufacturing!
The History of Robotics in Manufacturing
The history of robotics in manufacturing is a fascinating tale that dates back to the early 1960s. At that time, industrial robots were first introduced into factories for performing repetitive tasks such as welding, painting and handling heavy materials.
These robots were not as advanced as today's models but had basic programming capabilities that allowed them to follow pre-set instructions. In the following years, robotic technology improved significantly with the introduction of computer control systems and sensors.
By the 1980s, robots became more versatile and began to perform complex tasks such as assembling small parts and packaging products. This advancement led to increased efficiency in production lines, reduced labour costs and greater consistency in product quality.
As we entered into the new millennium, robotics continued to evolve at an unprecedented pace. Today's modern-day robots are equipped with artificial intelligence (AI) capabilities which allow them to adapt to changing environments without human interference. They also possess enhanced safety features making them safer than ever before for workers who work alongside these machines.
It's clear that robotics has come a long way since its inception over six decades ago. Its impact on manufacturing has been significant thus far - reducing errors and increasing productivity while providing a safer working environment for employees on factory floors worldwide!
The Types of Robots Used in Manufacturing
The use of robots in manufacturing has become increasingly popular in recent years, with a wide range of different robots being used for various tasks. One type of robot commonly used is the articulated robot, which essentially resembles an arm and can be programmed to perform specific actions.
Another type of robot that's frequently utilized in manufacturing is the cartesian coordinate robot. These robots move on three axes, allowing them to pick up and place items with precision. Collaborative robots are also becoming more common - these machines work alongside humans and have sensors that detect when people are nearby.
SCARA (Selective Compliance Assembly Robot Arm) robots are another option for manufacturers looking to automate their processes, as they're designed specifically for assembly tasks. Delta or parallel-link robots are known for their high speed and accuracy - perfect for industries like electronics where every second counts.
Mobile robots have become increasingly popular due to their versatility - they can navigate around a factory floor independently and complete a variety of tasks. With so many options available today, it's clear that robotics will continue to play an important role in modern-day manufacturing!
How Robotics Is Transforming Industry Standards
Robots have changed the game in manufacturing. With their ability to work tirelessly and efficiently, they are transforming industry standards for good.
One of the biggest ways robotics is changing things is through automation. By automating tasks that were previously done by humans, manufacturers can increase productivity while reducing costs. This means that products can be made faster and with greater precision than ever before.
Another way robotics is transforming industry standards is through safety. Robots can perform dangerous tasks like welding or handling hazardous materials without putting human workers at risk. This not only reduces workplace injuries but also lowers liability issues for manufacturers.
Additionally, robots are helping to improve quality control in manufacturing. They can inspect products for defects more accurately than humans, which means fewer defective items make it out into the market.
Robotics has opened up new possibilities in customization and personalization of manufactured goods. With robots capable of quickly adapting to different designs and specifications, companies can offer unique products tailored specifically to individual customers' needs.
These advancements show how much potential there still is for growth within this industry - all thanks to the power of robotic technology!
The Pros and Cons of Robotics in Manufacturing
When considering the implementation of robotics in manufacturing, it is important to weigh both the advantages and disadvantages. One clear advantage is increased efficiency and productivity. Robots can work continuously without breaks or fatigue, ultimately resulting in faster production rates.
Another benefit is improved safety for human workers as robots can perform dangerous tasks without risking injury or harm. Additionally, robotics technology allows for more precise and accurate operations which often results in higher quality output.
On the other hand, implementing robotics comes with a high initial cost of purchasing and integrating the technology into existing systems. There may also be job displacement concerns as some tasks previously performed by humans will now be automated.
Furthermore, maintaining and repairing robotic equipment requires specialized knowledge that may not always be readily available at all times leading to potential downtime issues. There are also limitations on what robots can do compared to human workers such as problem-solving skills or adapting to unexpected situations.
While there are certainly benefits to incorporating robotic technology into manufacturing processes, it is crucial for companies to carefully consider these pros and cons before making any decisions on implementation.
The Future of Robotics in Manufacturing
The future of robotics in manufacturing is exciting and full of potential. As technology continues to advance at an astonishing rate, so do the capabilities of robots used in manufacturing processes. In the coming years, we can expect to see even more sophisticated and specialized robots that are designed for specific tasks.
One area where we can expect significant growth is in collaborative robots or cobots. These machines work alongside human workers and are designed to be safe and easy to use. They have a wide range of applications, from assembly line work to material handling.
Another trend that will continue into the future is the integration of artificial intelligence (AI) into manufacturing robotics. AI allows robots to learn from their environment and make decisions on their own, which can increase efficiency and productivity while reducing errors.
In addition, we may see advances in 3D printing technology that allow for greater customization and flexibility in product design. This could lead to smaller production runs with faster turnaround times as well as reduced waste.
The future of robotics in manufacturing promises increased automation, improved safety standards, enhanced precision, decreased costs through streamlined processes - all leading towards sustainable development practices with higher economic returns. It's an exciting time for this industry!
As we have seen throughout this article, robotics has redefined the way manufacturing is done. With its high precision and efficiency, it has helped companies save cost and time. Robotics in manufacturing provides an opportunity for industries to improve their productivity while reducing errors, accidents, and injuries.
However, changing to robotics isn’t as simple as flipping a switch; it requires significant investment of capital, time and resources. Companies must be willing to train employees or even hire new ones with expertise in robotics technology.
The future of robotics in manufacturing looks bright with advancements such as artificial intelligence (AI), machine learning (ML) and cloud computing being integrated into robotic systems. This combination offers greater flexibility while making automation more intuitive than ever before.
The use of robots in manufacturing is transforming industry standards by increasing production rates while providing higher levels of accuracy that are unattainable through manual labor. The benefits outweigh any cons associated with implementing these machines on factory floors around the world today!
Comments
Post a Comment